Permanent magnet rotor e1655961736623.jpeg.
The rotor overtemperature caused by losses is one of the important issues for the high-speed electrical machine. This paper focuses on the rotor loss analysis and CFD-thermal coupling evaluation for 105 kW, 36,000 r/min HSPMSM. Three types of sleeve materials as carbon-fiber, Titanium alloy, and stainless steel are introduced in this paper, …
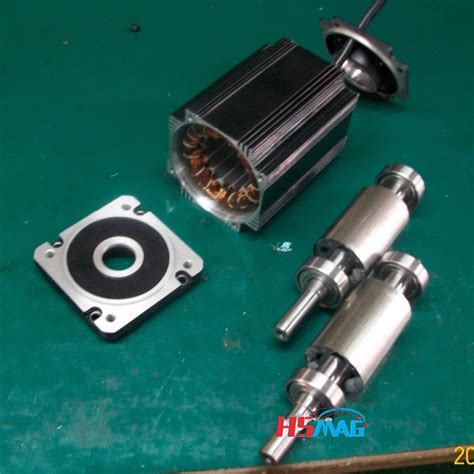
The traditional bearingless synchronous reluctance motor (BSynRM) with salient pole rotor has some drawbacks such as high suspension force ripple, low torque density and low power factor. To overcome the above shortcomings, the permanent-magnet-assisted bearingless synchronous reluctance motor (PMa-BSynRM) is …An ironless rotor structure wastes permanent magnet material, since the magnetic circuit closes through air in the rotor side. Therefore, a thin steel rim, to which the magnets are attached, is employed (Fig. 9.1) The rim can be either a laminated structure, in which case the eddy current losses of the rotor remainNon−Magnetic Rotor Core Rotor Magnets Rotor Pole Pieces Figure 2: Axial View of a Flux Concentrating Motor The geometry of one type of internal magnet motor is shown …This paper proposes a two-phase radial flux brushless DC motor comprising a rotor decorated with hybrid permanent magnet (PM) material, i.e., rare-earth NdFeB magnets combined with ferrite magnets. The rare-earth NdFeB magnets are used on the surface, and ferrite magnets in the spoke-type configuration. The combined surface and …In this paper, a novel dual mechanical port dual rotor counter-rotating permanent magnet flux switching generator (DMPDRCR-PMFSG) for wind turbine applications is proposed. Power distribution between the inner and outer rotors of the proposed DMPDRCR-PMFSG that contributes to the cumulative output power is …
Mar 16, 2015 · A post-assembly magnetizing fixture has been designed and successfully used to magnetize the rotor of a 100 kW high speed permanent magnet synchronous motor. The rotor is a solid cylinder with outer diameter of 80 mm and total length of 515 mm. The permanent magnet material is samarium-cobalt (Sm 2 Co 17) with saturation magnetizing field of 6 ... where B m is the maximum air gap flux density (0.4–0.9 T), B r,m is the remanence flux density of the magnets (1.2 T) at the operating temperatures of the outer rotor PMSG, is the relative permeability of the …Aug 5, 2020 · To enhance the torque density of a permanent magnet (PM) motor, a rotor overhang structure (OS), which is a simple and effective way to increase the flux linkage, is used in various types of PM motors such as SPM motors [5-9], interior PM motors , and spoke-type PM motors [11, 12]. The OS means that the axial length of the rotor is designed to ...
1 Introduction. Flux-switching permanent-magnet (FSPM) motors have advantages such as high-power and -torque density, high efficiency and simple and robust mechanical structure in the rotor [1-4].These motors have bipolar flux linkage and sinusoidal back-electromotive force (EMF) [].In FSPM motors, because of the placement of …
A permanent magnet rotor assembly is a crucial component in various applications, including BLDC motors, generators, and magnetic couplings. It consists of a rotor with permanent magnets, such as neodymium magnets, mounted on it to ensure an efficient and reliable magnetic field generation. The interaction between the magnetic field …The permanent magnet synchronous motor (PMSM) is widely used in the electric vehicle and domestic appliance industries. The structure of the PMSM motor varies depending on the permanent magnet arrangement in the rotor structure; among them, the interior permanent magnet (IPM) PMSM motors made by inserting permanent …An interior permanent magnet synchronous motor (IPMSM) with ‘VV—’ shape rotor topology structure is proposed. The established two-dimensional (2D) parameterized finite element analysis (FEA) models are used to analyze and compare the output average torque, torque density, air-gap flux density and back electromotive force …Permanent magnet motor. Schematic of a permanent magnet motor. A permanent magnet motor is a type of electric motor that uses permanent magnets for the field excitation and a wound armature. The permanent magnets can either be stationary or rotating; interior or exterior to the armature for a radial flux machine or layered with the armature for ...
1. Introduction. At present, the low-speed high-torque transmission system has vast application prospects in the application fields of ship propulsion, lifting, mining and oil field exploitation [1].Permanent magnet motors can maintain good performance in a wide range of load changes, so they have received extensive attention in low-speed and large …
Dec 15, 2023 · Interior permanent magnet (IPM) motors in traction applications often employ discrete rotor skewing constructions to reduce torsional excitations and back-EMF harmonics. Although skewing is very effective in reducing cogging torque, the impact on torque ripple is not well understood and can vary significantly over the operating envelope of a motor. Skewing also leads to the creation of a non ...
The most obvious performance difference is that a PMAC motor rotates at the same speed as the magnetic field produced by the stator windings, meaning it is a synchronous machine. If the field is “rotating” at 1800 rpm, the rotor turns at the same speed. An induction motor, on the other hand, is considered an asynchronous machine. An internal permanent magnet synchronous machine (IPMSM) was designed for heavy-load traction vehicles applied in port transportation. Based on finite element analysis (FEA), the rotor iron core topology was optimized with the most attention paid to cogging torque and torque ripple. The influences of the iron core on the air-gap …A Permanent Magnet DC motor (PMDC motor) is a type of DC motor that uses a permanent magnet to create the magnetic field required for the op...Jun 23, 2022 · The rotor overtemperature caused by losses is one of the important issues for the high-speed electrical machine. This paper focuses on the rotor loss analysis and CFD-thermal coupling evaluation for 105 kW, 36,000 r/min HSPMSM. Three types of sleeve materials as carbon-fiber, Titanium alloy, and stainless steel are introduced in this paper, researching the effects of sleeve conductivity ... Based on the complex structural characteristics of permanent magnet-assisted synchronous reluctance motors (PMA-SynRMs), this paper proposes a multi-objective optimization design method for the motor using a composite algorithm. Firstly, the power density, electromagnetic torque, cogging torque, and torque fluctuation coefficient …Dec 2, 2022 · This paper presents an analytical method for calculating rotor stresses of high-speed surface-mounted permanent magnet synchronous motors (SPMSMs) with segmented permanent magnets (PMs), the pole-arc coefficient, fillings between poles, and material anisotropy are accurately considered. Afterward, the rotor stresses with different retaining sleeves and fillings are compared, the variation laws ...
Sep 17, 2020 · Differently from the surface-mounted permanent magnet (PM) synchronous motors, there is an asymmetry of the reluctance between the d-axis and the q-axis, in which saliency can be used to produce reluctance torque in addition to the magnet torque, thus improving the efficiency. In addition, the IPMSMs provide more rotor robustness as magnets are ... In this paper, an optimal design procedure which includes multi-physics analysis to design the multi-phase external rotor PMa-SynRMs is presented. In specific, a five-phase external rotor PMa-SynRM with neodymium based magnets has been proposed as a solution to produce higher power density compared to the conventional internal rotor PMa-SynRMs ...Axial flux permanent magnet synchronous motors (AFPMSMs) have been widely used in wind-power generation, electric vehicles, aircraft, and other renewable-energy applications owing to their high power density, operating efficiency, and integrability. To facilitate comprehensive research on AFPMSM, this article reviews the developments in …Jan 8, 2021 · The permanent magnet is axially magnetized; meaning that the north and south poles alternate and are on the same axis as the motor shaft. When current is applied to windings, poles on the stator are magnetized and align with the opposite poles from the permanent magnet rotor. For example, north poles would align directly across from south poles. In a permanent-magnet machine, where the magnets reside on the rotor, there is no secondary winding. However, the permanent magnet can be modeled with a fictitious secondary winding excitation [1,2] and therefore the stator leakage inductance can be defined. Care must be taken that permanent magnets do not get demagnetized due to excessive ...
The accurate initial rotor position of a permanent magnet synchronous motor (PMSM) is necessary for starting the motor, and for the position sensorless control method adopted by a PMSM control system under some working conditions. This paper presents a new method to detect the initial rotor position of a permanent magnet synchronous motor (PMSM). …Permanent-Magnet Motors Wen L. Soong, Member, IEEE, and Nesimi Ertugrul, Member, IEEE Abstract— This paper compares the field-weakening perfor-mance under rated and overload conditions of synchronous reluctance and interior permanent-magnet motors against that of a baseline 2.2-kW induction machine. Four prototype rotors based
Today’s automotive industry has focused its studies on electric vehicles (EVs) or hybrid electric vehicles (HEVs) rather than gasoline-powered vehicles. For this reason, more investment has been made in electric motors with high efficiency, high torque density, and high-power factor to be used in both EVs and HEVs. In this study, an outer-rotor …Permanent Magnet Rotors High-Speed, High-Reliability, High-Efficiency Permanent Magnet Rotors For over 25 years, Integrated Magnetics has developed and refined the …In this work we proposed to study the use of permanent magnet synchronous motors (PMSM) for railway traction in the high-speed trains (HST) of Renfe Operadora (the Spanish national railway operator). Currently, induction motors (IM) are used in AVE classes 102–112 trains, so, the IM used as a traction motor in these trains has …A Permanent Magnet DC motor (PMDC motor) is a type of DC motor that uses a permanent magnet to create the magnetic field required for the op...Summary. PM (Permanent Magnet) Type: uses permanent magnets, moderate torque, low to mid-speed. VR (Variable Reluctance) Type: toothed rotor/stator, low torque, mid to high speed. Hybrid Type: combines permanent magnets and teeth, good combination of torque and speed.Sep 2, 2020 · In the PMSG that has not been the CT reduction technique, the rotor permanent magnets (PMs) have an increasing effect on the CT since each PM has the same relative position with reference to the stator slots . The CT in each PM is in the same phase as the others, so, the harmonic component of each is added together then, CT has become higher. A high-speed (HS) permanent magnet (PM) synchronous motor (HSPMSM) with a carbon fiber-reinforced plastic (CFRP) protective sleeve in the surface-mounted rotor was explored in this study.In order to get rid of the bulky and lossy differential gears and to enhance the system robustness, the magnetic differential (MagD) system is proposed after the mechanical differential (MechD) and electronic differential (ElecD) systems. The MagD system is mainly composed of the double-rotor (DR) stator-permanent-magnet (PM) …
Permanent Magnet Motors - External Rotor. The W series external-rotor permanent magnet motor combines the high strength alloy material with the patented one-piece fan …
A permanent magnet rotor assembly is a crucial component in various applications, including BLDC motors, generators, and magnetic couplings. It consists of a rotor with permanent magnets, such as neodymium magnets, mounted on it to ensure an efficient and reliable magnetic field generation. The interaction between the magnetic field …
This paper proposes a new structure of the dual-rotor hybrid-excited axial-flux permanent magnet vernier machine (DR-HEAFPMVM) with the modular stator and the consequent-pole PM (CPM) rotor for low-speed, high torque density applications such as in-wheel electric vehicles. The tooth-wound non-overlapping armature windings and direct …Based on the complex structural characteristics of permanent magnet-assisted synchronous reluctance motors (PMA-SynRMs), this paper proposes a multi-objective optimization design method for the motor using a composite algorithm. Firstly, the power density, electromagnetic torque, cogging torque, and torque fluctuation coefficient …Today’s automotive industry has focused its studies on electric vehicles (EVs) or hybrid electric vehicles (HEVs) rather than gasoline-powered vehicles. For this reason, more investment has been made in electric motors with high efficiency, high torque density, and high-power factor to be used in both EVs and HEVs. In this study, an outer-rotor …Magnetization process for PM rotors. The Permanent Magnet (PM) motor is a critical part in many electric car powertrain designs, which is undergoing rigorous improvement and changes. PM motors offer compact design and higher system efficiency among other advantages. The race for the electric cars has begun in the automotive industry and ... Dec 15, 2023 · Interior permanent magnet (IPM) motors in traction applications often employ discrete rotor skewing constructions to reduce torsional excitations and back-EMF harmonics. Although skewing is very effective in reducing cogging torque, the impact on torque ripple is not well understood and can vary significantly over the operating envelope of a motor. Skewing also leads to the creation of a non ... Choosing the proper engine that fits the desired application is a crucial design factor in robotics. Accordingly, this paper compares different types of engines for other Industrial robots (IR) and proposes to put practical criteria based on the mechanical design and its application. It starts from describing the IR choice to explaining the …The permanent magnet motor tends to have larger step angles, 7.5° or 15°, than the variable reluctance motor. The hybrid motor typically has 200 rotor teeth and rotates at 1.8° step angles. They have high static and dynamic torque and can run at very high step rates. As a consequence they are very widely used. Dec 1, 2017 · In their work, a range of electric machine options are considered and it is concluded that a synchronous machine with a permanent magnet (PM) rotor will be the most efficient and power dense. In addition to applications in turbocharging, Gerada [ 3 ] highlight an increasing demand for high-speed electrical machines in flywheel energy storage ... Machines incorporating high-speed electrical machines (HSEM) are becoming increasingly common place in applications including air handling, energy storage and medical devices. They are of increasing interest within the automotive field for air handling applications. HSEM’s use surface-mounted permanent magnet (PM) rotors, manufactured from rare …Conventional high-speed flux-switching machines have either a high fundamental frequency or more even harmonics. This paper proposes a novel six-slot four-pole axial flux-switching permanent magnet machine for high-speed applications. The machine, consisting of two radially distributed stators and one rotor, can effectively …Arnold produces high performance permanent magnet motor components and sub-assemblies for aerospace and defense, industrial, automotive, and motorsport applications, such as: KERS — Kinetic Energy Recovery …
The accurate initial rotor position of a permanent magnet synchronous motor (PMSM) is necessary for starting the motor, and for the position sensorless control method adopted by a PMSM control system under some working conditions. This paper presents a new method to detect the initial rotor position of a permanent magnet synchronous motor (PMSM). …The traditional bearingless synchronous reluctance motor (BSynRM) with salient pole rotor has some drawbacks such as high suspension force ripple, low torque density and low power factor. To overcome the above shortcomings, the permanent-magnet-assisted bearingless synchronous reluctance motor (PMa-BSynRM) is …An interior permanent magnet synchronous motor (IPMSM) with ‘VV—’ shape rotor topology structure is proposed. The established two-dimensional (2D) parameterized finite element analysis (FEA) models are used to analyze and compare the output average torque, torque density, air-gap flux density and back electromotive force …Instagram:https://instagram. videos x en francaislaura dernavh 120bt wiring diagramblocked where Φ is the magnet flux crossing the air gap, R is the total reluctance through the flux paths and θ is the rotor angle. It is clear that if the reluctance R does not vary as the rotor rotates, then the cogging torque T cog is zero. From this point of view, the cogging torque can be improved by changing the V-shape rotor structure variables … sweatshirts 601638rosk an interior permanent magnet (PM) synchronous motor into a hybrid motor. This hybrid technology uses a conventional induction rotor cage to bring the motor up to its slip speed just like any traditional induction motor. Once at slip speed, the powerful interior magnets pull the rotor into true synchronous speed with the rotating magnetic field. 5651 optimize the subject line in a campaign email The SPMSM has the permanent magnets fixed on the surface of the rotor leading to a symmetrical radial air-gap reluctance path between the rotor and the stator core. The IPMSM has the permanent magnets inserted inside the rotor core leading to a non-symmetrical radial air-gap reluctance path between the rotor and the stator core. This control method can control the AC permanent magnet servo motor as a DC permanent magnet motor in a sense. According to Equations (1)–(3), the second-order dynamic equation of the position ring of the PMSM is expressed as follows: (4) { θ ˙ = ω ω ˙ = b i q + d (4) where b = 1.5 p n ψ f / J is a disturbance composed of unknown friction …Dec 15, 2023 · Interior permanent magnet (IPM) motors in traction applications often employ discrete rotor skewing constructions to reduce torsional excitations and back-EMF harmonics. Although skewing is very effective in reducing cogging torque, the impact on torque ripple is not well understood and can vary significantly over the operating envelope of a motor. Skewing also leads to the creation of a non ...